フロントカウル貼りこみ(2016年9月下旬)IF-02RDS ロードバージョン開発経過 [Ikeya Formula IF-02RDS]
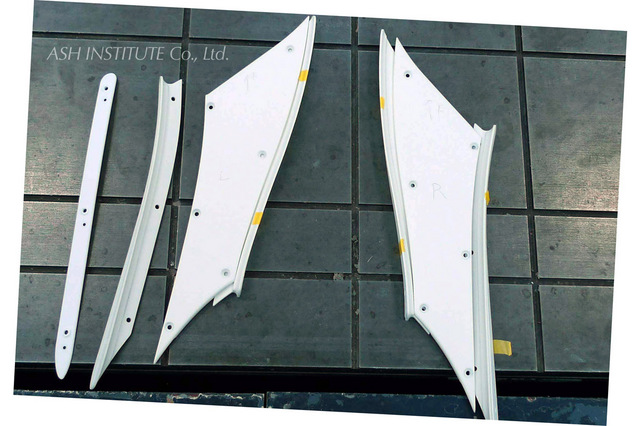
上の画像はフロントカウルとフロントフェンダーをつなぐパーツで、普通の車ではこんなパーツは無いので
一般的な名前が無い。名前が無いと何かと困るので便宜上フロントフェンダーブリッジと呼んでいる。
最初のデザインをするときに池谷さんからリクエストされた数少ない項目のひとつ、フロントカウルの
いわゆるノーズに相当する部分はなるべく細身に、ということを考慮した形状になっているフロントカウルと、
それとは独立したボリュームのフロントフェンダーを上部で固定するためのもので、デザインを成立させて
剛性も確保するために必要なパーツ、ということになる。
1号車からはフロントウインドーの形状が保安基準を満たすために変わり、横幅が広がった。それに合せて
フロントカウルも形状が変わり、フロントフェンダーも内側にあった穴というか切り欠きがなくなり、
フルステアしたときのタイヤが干渉しないように幅が広がった。
(1号車のときは、これも数少ない池谷さんからのリクエストのひとつなのだが、フロントフェンダーは
なるべくスリムに、というのがあって、それとフルステアしたときのタイヤとフェンダー内面の干渉を防ぐ
ために穴、切り欠きを設けていた)
両者の幅が広がったので、その間隔は狭まり、そこをつなぐこのパーツも幅の狭い小型なものになった。
大きさとしては小さいのだが、細かい設計要件がいろいろあって、内部に頭の形状が特殊なボルトを仕込んで
いたり、下面にやはり薄型で特殊なナットを仕込んでいたりして、これを手作業のFRPで作るのは至難の業
(事実上不可能)なので、これは粉末造形で作ることにした。いわゆる3Dプリントの1種である。材質は
ナイロン系の樹脂で、粘りがあって割れにくく、十分丈夫なもの。この特性が個人的にかなり気に入っていて、
この車の他の部分でもいくつか使っている。
3Dプリンターが脚光を浴び始めた頃、何でもできるみたいに喧伝されたものが、決してそんなことは無い。
たしかにいい面はあるが、そんなうまい話があるわけ無かろうに…と、ややさめた目で見ていた。
少なくとも私の仕事で使うには、人手による表面仕上げが不可欠なのだが、このことを理解していない人は多い。
ただ、切削などの従来の製法では不可能なことが出来るのは確かだし、出来上がったものをそのまま機能部品と
して使えるのがいい。もちろん材質上の問題が出ない範囲の使い方でという限定付きだが、それでもいい。
非常にいい。
フロントカウルの成形型。
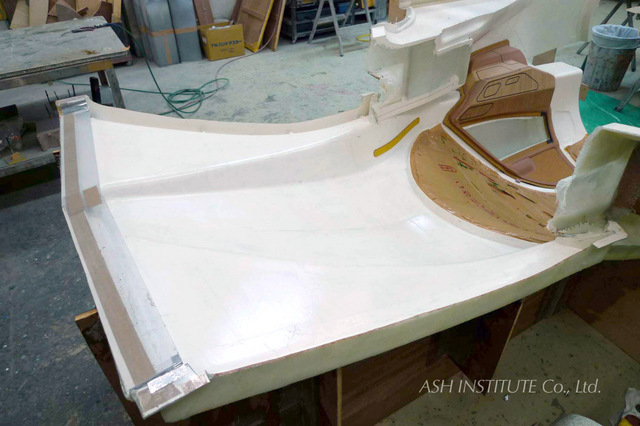
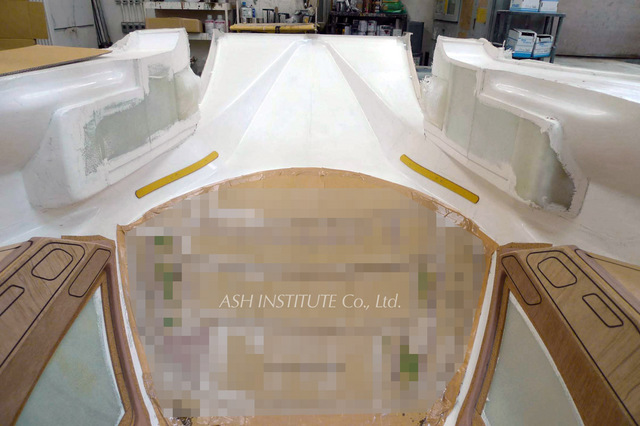
このアルミ箔を張った部分に、最初の写真にあったフロントフェンダーブリッジの座面に相当する部分が
取り付けられる。
取り付けた状態で表面が滑らかにつながるように、一般面から1段落ちたへこみになっている。
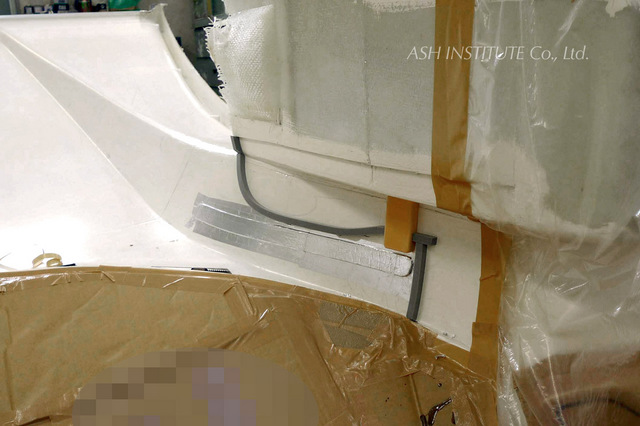
離型処理をして、ゲルコート塗って、FRPを貼りこんで、硬化したらトリミング。
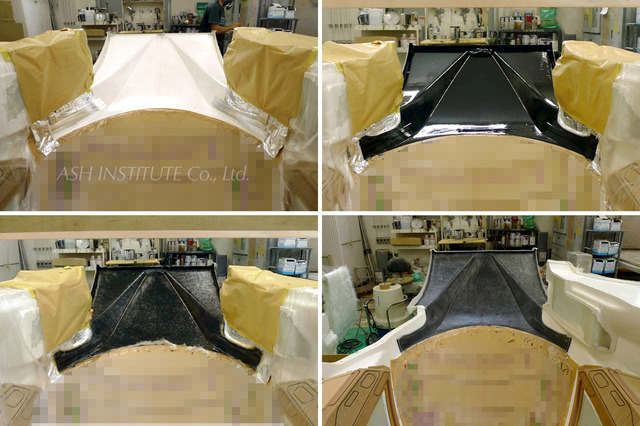
成形できたフロントカウル。
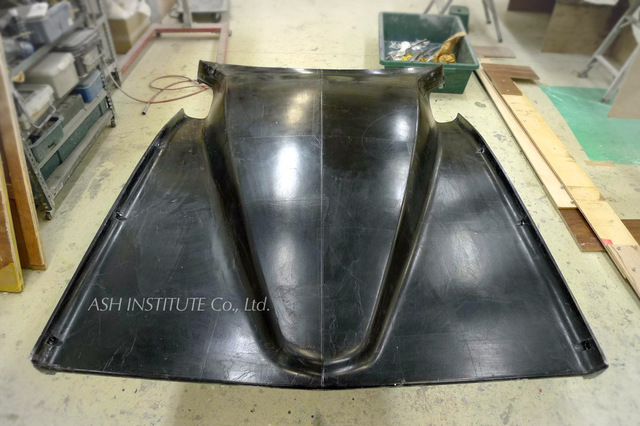
写真は全て、この作業をお願いしている NY Connect の内藤さん撮影。
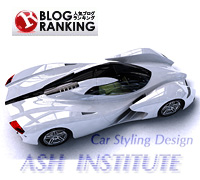
リヤカウルインナーパネル造形、型取り(2016年9月下旬)IF-02RDS ロードバージョン開発経過 [Ikeya Formula IF-02RDS]
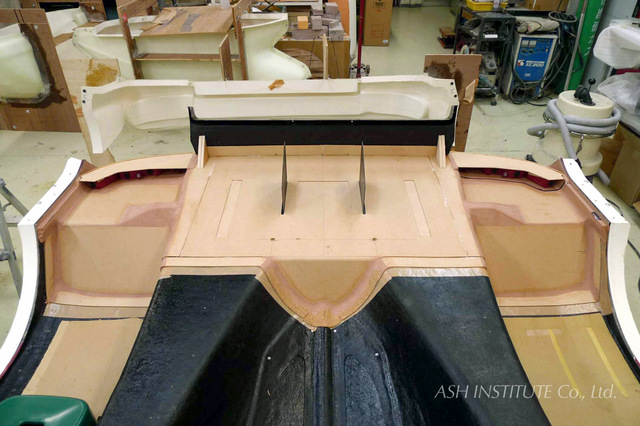
リヤカウルは保安基準に触れるところはないので1号車からキャリーオーバー。使用すリヤコンビランプが
変わるのでそれに関連するところとホイールアーチまわりをすこし修正するが基本的には1号車のままの形状。
ただ、1号車を作った時にリヤカウルはもっと剛性を上げたいと思っていたのと、あけたときに見える裏面の
仕上げ(FRP貼りっぱなし)が気になっていたので、これらを同時にグレードアップしようということで、
インナーパネルを新設することにした。とはいってもこの大きなリヤカウル全面ではなくて後半部分のみ。
新しいリヤコンビランプを固定するためのマウントとしても機能する。
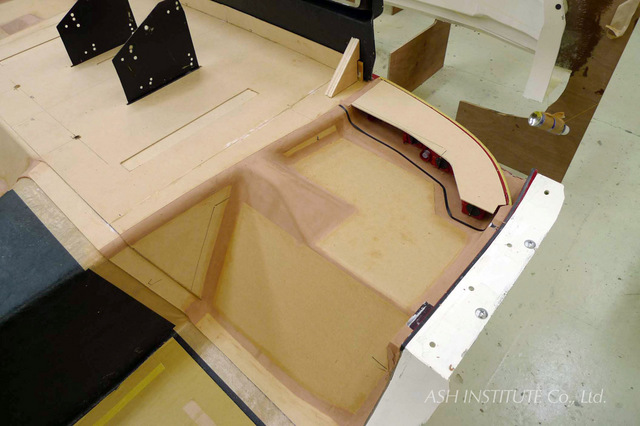
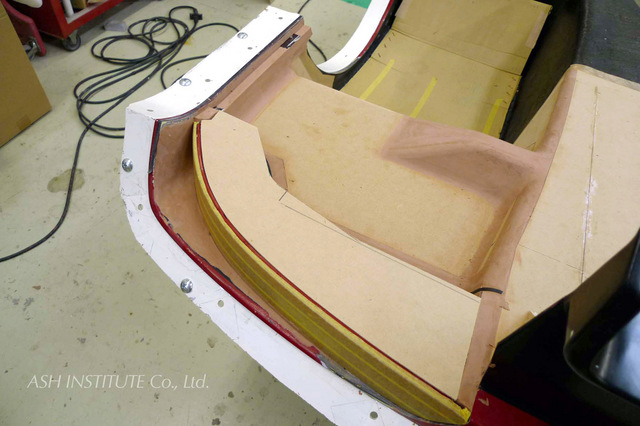
リヤウイングのマウントステーがリヤカウルの真ん中を貫通する構造なので、インナーパネルはこれをよける。
平面に近いところは合板で、平面と平面をつなぐところや曲面部分はクレイで造形。
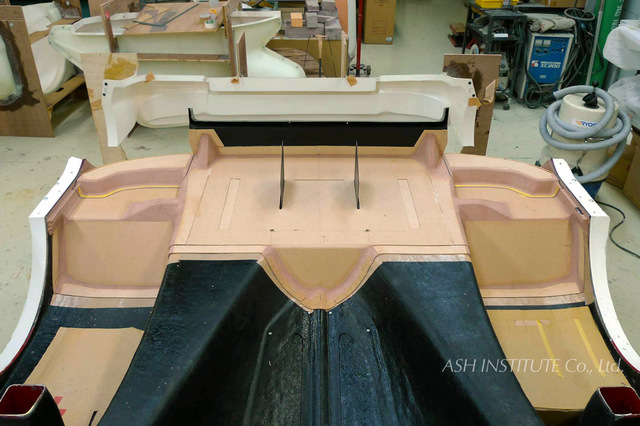
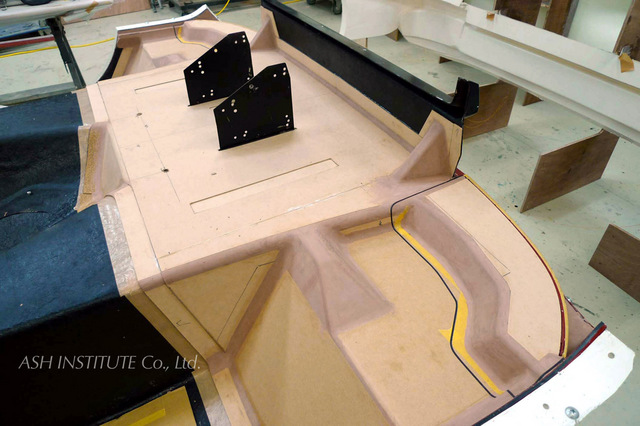
造形が出来たら、各パーツごとに型取り。
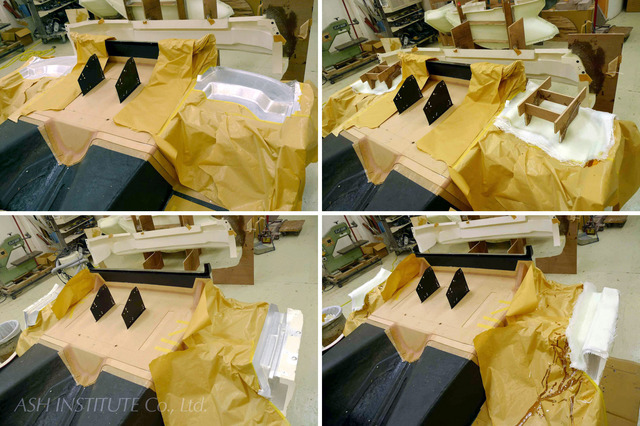
ひとつ前の記事でも書いたが、こういったインナーパネル、補強のたぐいも、できることなら全て面データを
活用してNC切削でマスターモデルを作るとか、3Dプリント(粉末造形等)で直接成形するとかしたいもの
ではある。
ただ、1号車で気になっていたところに手を加えて、少しでも改善できるのは嬉しい。2号車(それ以降も
含めて)を作れるということは、そのチャンスをいただけたこと自体とてもありがたいことだと思う。
写真は全て、この作業をお願いしている NY Connect の内藤さん撮影。
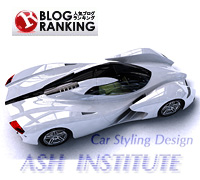
ドア貼りこみ、インナーパネル造形(2016年9月上旬~9月中旬)IF-02RDS ロードバージョン開発経過 [Ikeya Formula IF-02RDS]
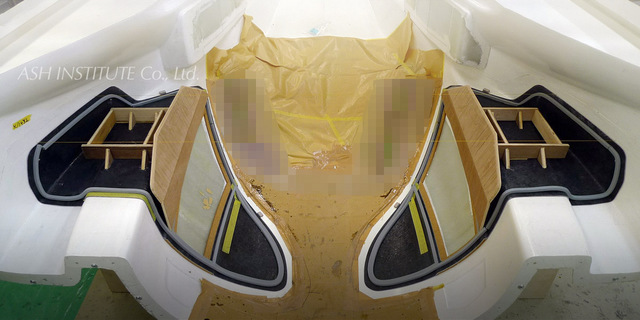
成形型が出来たのでいよいよFRPの貼りこみ。
まずは開口部、ドアから。

FRPを貼りこんだら、補強を兼ねたインナーパネルの造作をウレタンや合板、クレイなどで行っていく。

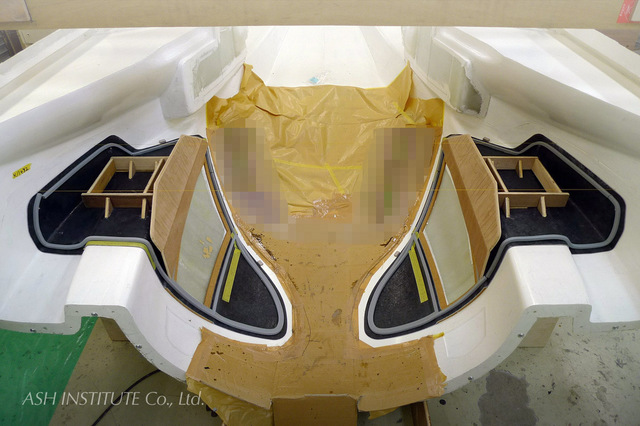
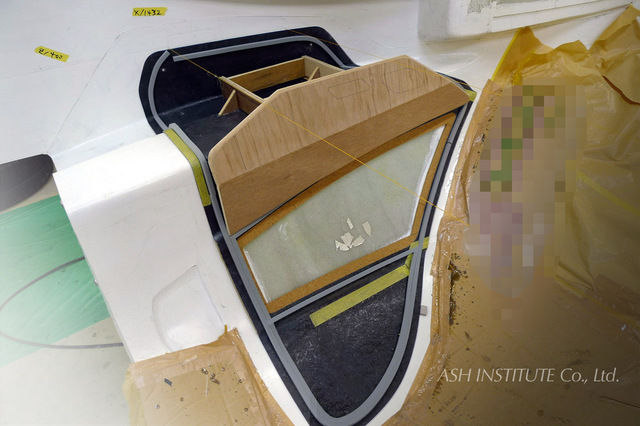
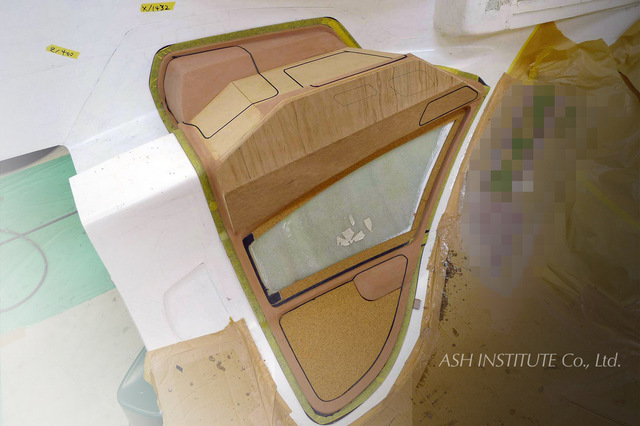
マーキングしてある部分はサービスホールや、別パネルとして取り外しできるようにする部分、
インナードアハンドルの取り付け位置、ドアを閉めるときにつかむグリップに相当する部分など。

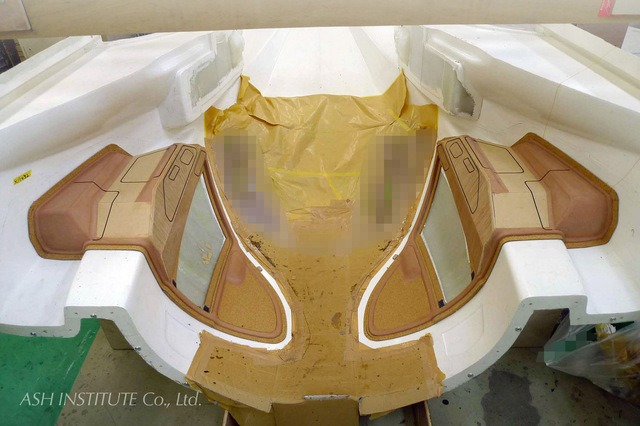
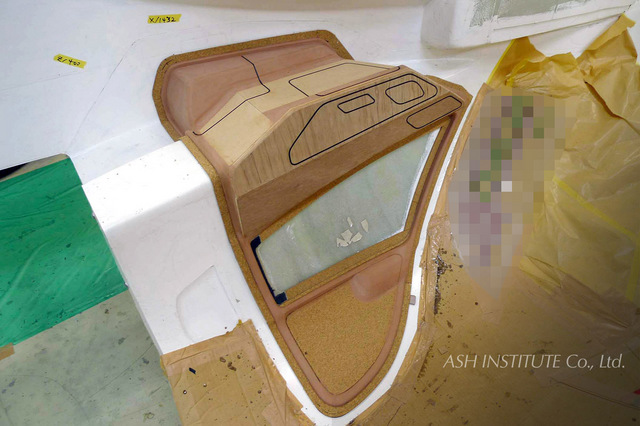
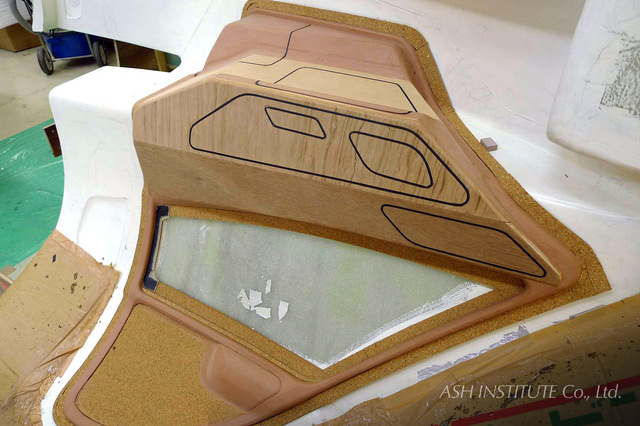
これらの作業も、できることなら面データを活用してNC切削や3Dプリント(粉末造形等)で全てまかない
たいところなのだが、このような製法をとっている理由は…
この車の場合、1号車では各機構を保持する造作があるだけで、まともなインナーパネル自体が無かった。
2号車でも当初は同様な構成で行こうと思っていたのだが、ごく少数とはいえ何台か作ることや、市販化を
考えると、やはりあったほうが良い、ということで、途中で作ることになった。
しかしながら、1号車のリヤカウルをほぼキャリーオーバーし、新たに作るキャビンはクレイモデルを
作って手作業によってリヤカウルとの整合を図る、というエクステリアの製法から、データとの完全な
整合が保証できないこともあり、このようにモデラーのスキルに大きく依存するやり方になっている。
開発コストを抑えるために、活かせる物はなるべく活かして、極力大掛かりなことにならないように…、
という発想。
しかしながら作業が進めば進むほど、解決すべき要素がワラワラ出てきて、この方法が本当に正しいのか
どうか、不安になってくるのも確か。 解決すべき要素が多すぎる、だがギャンブルは出来ない…。
実は同時に開発しているもう1台の車では、エクステリアのボディパネルは全てCFRP製(いわゆるドライ
カーボンでハニカムをサンドイッチしたもの、少し前にほぼ完成済み)としていて、こちらはほぼ完全に
データを再現しているもので、上記のインナーパネル類も全てデータから直接成形するやり方にしようと
思っている。これはいくつかの理由があって当初の想定とは違うし、データ作成の工数はちょっと想像
したくないほどのものになるだろうが、いつかやってみたいと思っていたことでもあるので、私の作業と
しては(非常に)きついがラッキーなことだと思う。
来年の春、あるいは初夏の頃、いやもっとずれ込むかもしれないが…、これらがその全ての工程を
終えた時、結果として両者のコストが比較できる、貴重なケーススタディになるかもしれない。
それは少しばかり楽しみなようにも思えるが、当然のように不安要素は山ほどあって、そちらのほうが
はるかに大きい。
写真は全て、この作業をお願いしている NY Connect の内藤さん撮影。
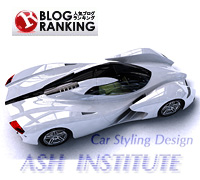
フロントフェンダー型取り(2016年8月末~9月上旬)IF-02RDS ロードバージョン開発経過 [Ikeya Formula IF-02RDS]

メインボディとは別にフロントフェンダーは独立したかたまりとして、左右それぞれ型取り。
内側のピーク付近で型を分割。まずは内側から貼りこみ。
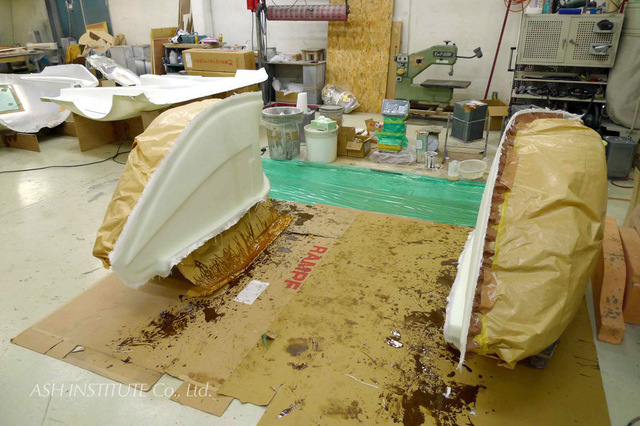
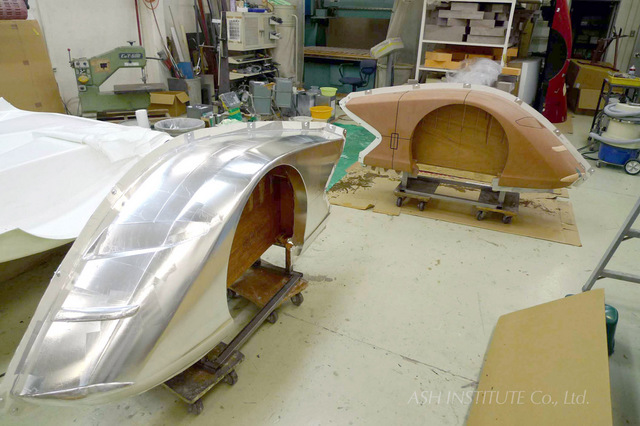
続いて外側も貼りこみ。
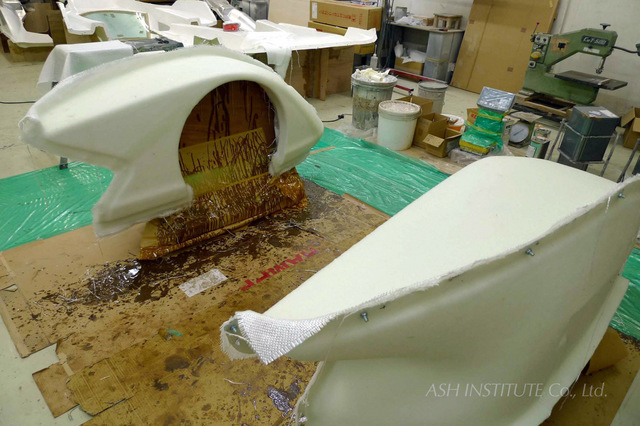
合板による補強。要領はメインボディと同様。補強合板の上面は高さがそろえられている。
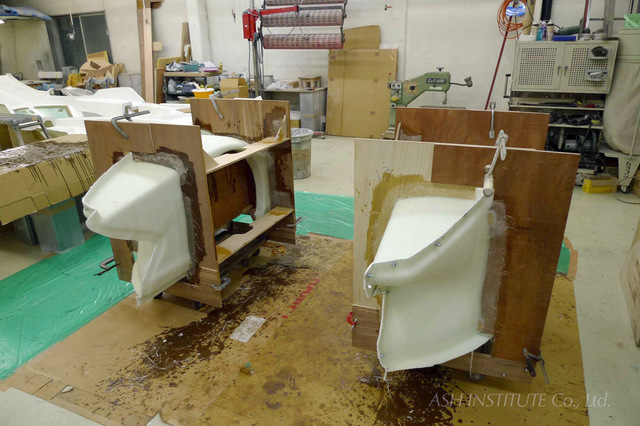
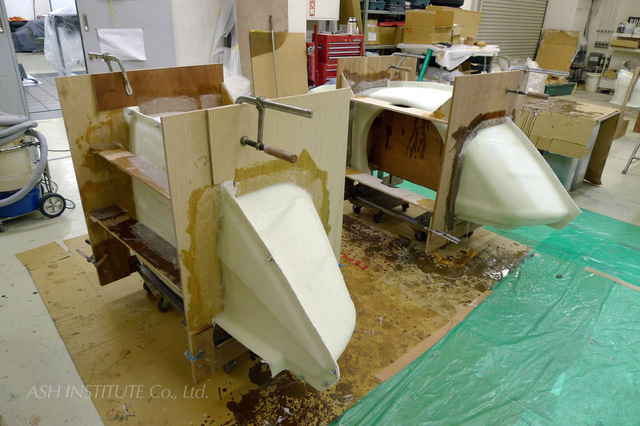
ひっくり返すとこんな感じ。
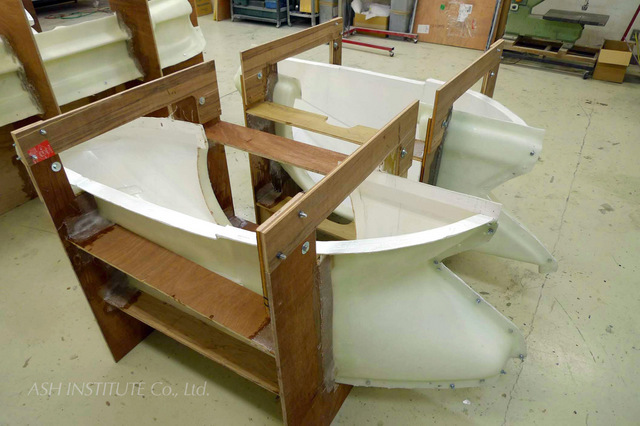
トータルの工数やコストを考えれば独立したフェンダーはいいものではない、とは重々思うのだが、
このデザインは一体成形では成立し得ないところがあるし、それがこの車の特徴的なところでもある。
何を優先するか、出来ることの中で最善の方法を考えた結果、これらはこういうことになっているわけだが、
“これでいいかな?本当にこれが最適解なのかな…?” そういう思いはここに限らず、ずっとついてまわる。
写真は全て、この作業をお願いしている NY Connect の内藤さん撮影。
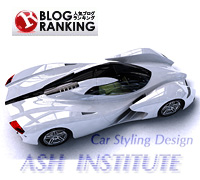
成形型脱型(2016年8月末~9月上旬)IF-02RDS ロードバージョン開発経過 [Ikeya Formula IF-02RDS]
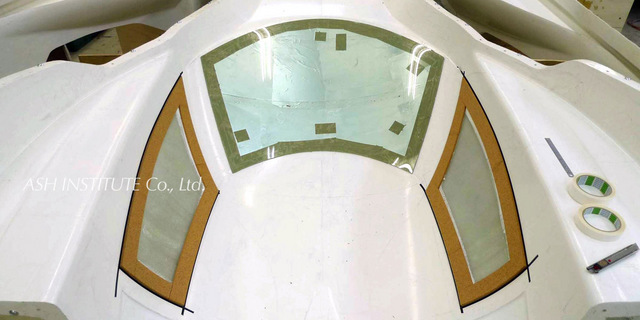
無事、脱型が済み、役目を終えたクレイモデル。
一般面はそうでもないが、外側のエッジ部分の損傷が多い。
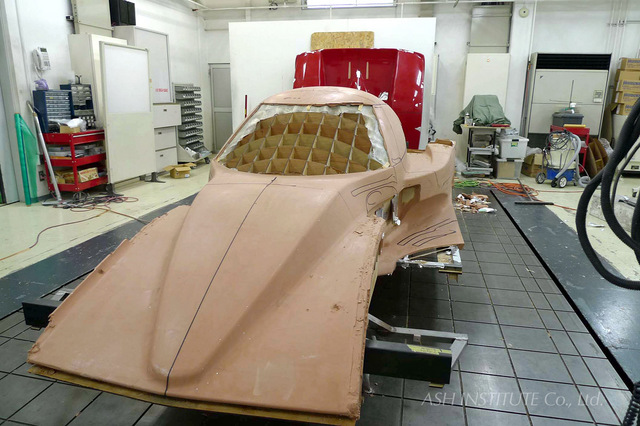
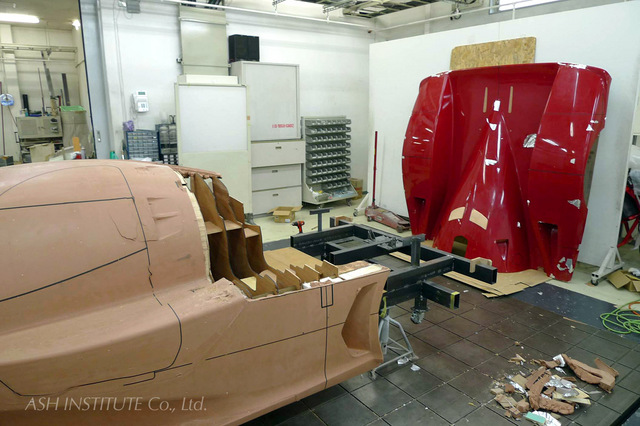
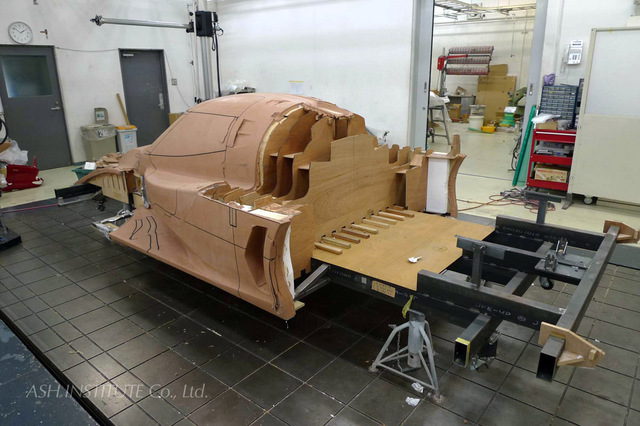
今回はたまたまフロントウインドーに本物を仕込んだまま型取りを行ったが、普通はこの種の段落ちの
造作にはシートワックスなどを使う。
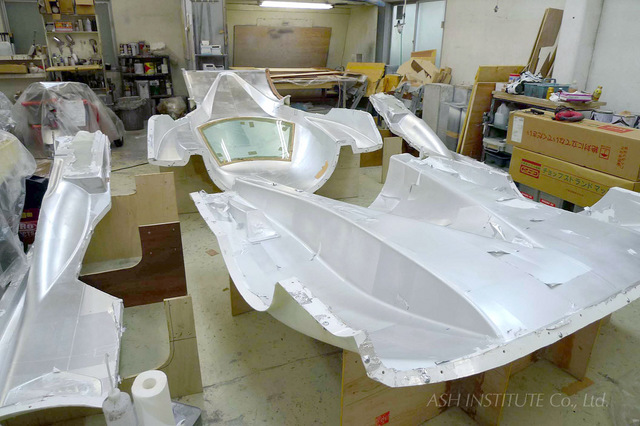
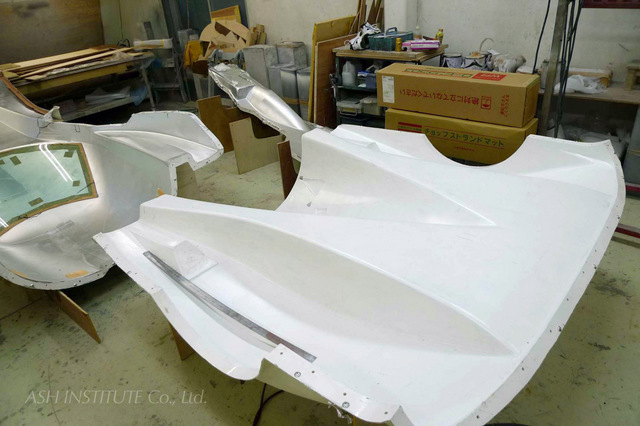
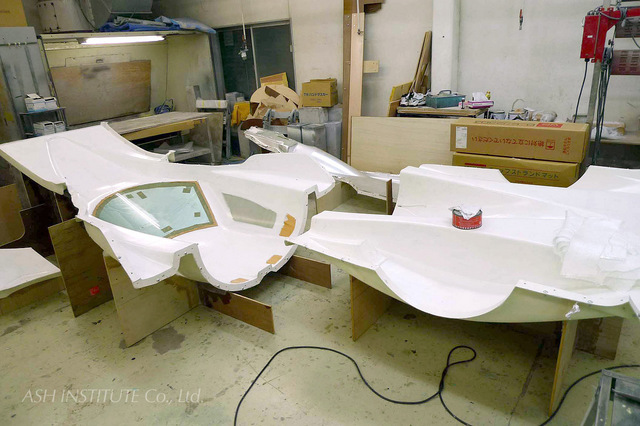
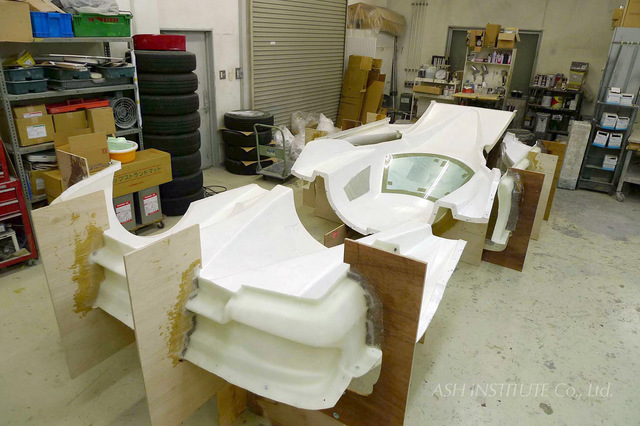
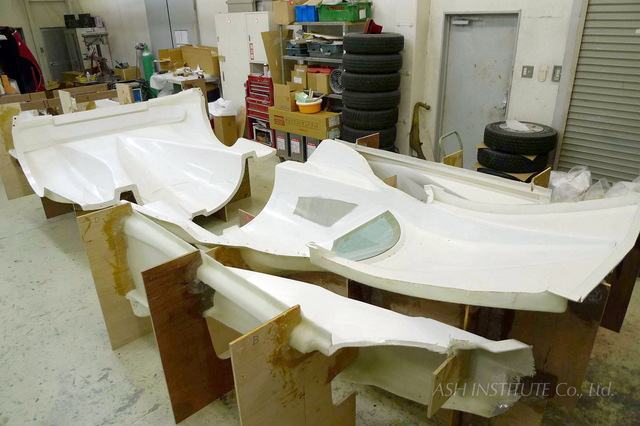
と、書いておきながらだが…、サイドウインドー用の段落ちの造作に今回使ったのはコルク(?)製の薄板。
均一な段落ちが出来て、ある程度の柔らかさ、弾力性があって、樹脂への耐性があればいいわけだ。
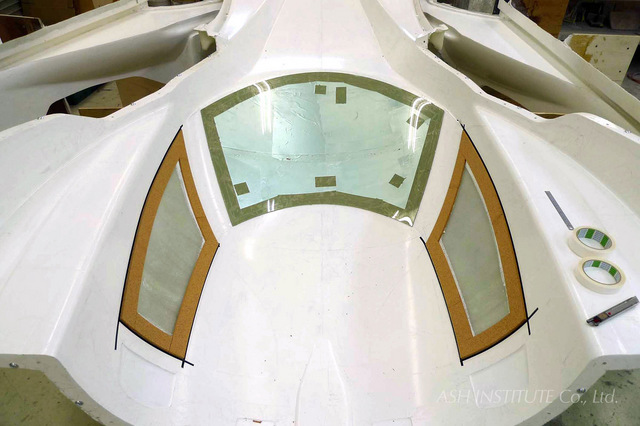
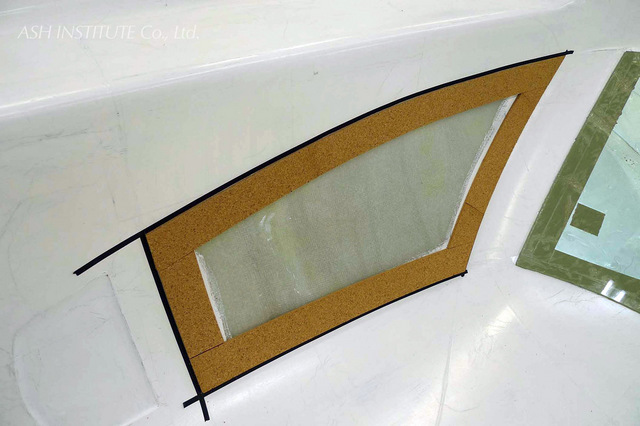
ドア周りのマスキングをして、ドアパネルの貼りこみ準備。
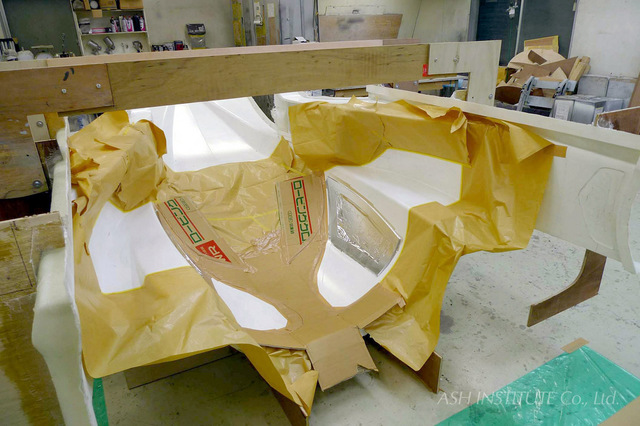
このあたりの工法は1号車とそれ程変わらず、個人的にはもう少し量産体性に近づけたいと思っていたところ
ではある。1号車同様に開発費を抑えるためにこういった工法にしたわけだが、クレイモデルをマスターモデル
代わりとする限り、成形型に加える造作はどうしても減らせない。それどころか、ごく少量とはいえ複数台を
作ろうとすると、この段階でやっておかなければいけない、やっておいたほうがいいと思われることが増え、
しかもその作業はモデラーのスキルに頼る面が大きくならざるを得ない。これをやらないと、再現性の無い、
ばらつきの大きなものになるし、何台作ろうがその決して良くない効率の作業工数が減らせない。
開発費を抑えれば製品単価は高くならざるを得ない(1個1個を作るための工数が多くかかったままということ)
というあたりまえのことなのだが、理解してもらいにくい面もあって、そこは苦しいところ。
写真は全て、この作業をお願いしている NY Connect の内藤さん撮影。
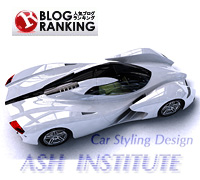
型取り(2016年8月中旬~下旬)IF-02RDS ロードバージョン開発経過 [Ikeya Formula IF-02RDS]
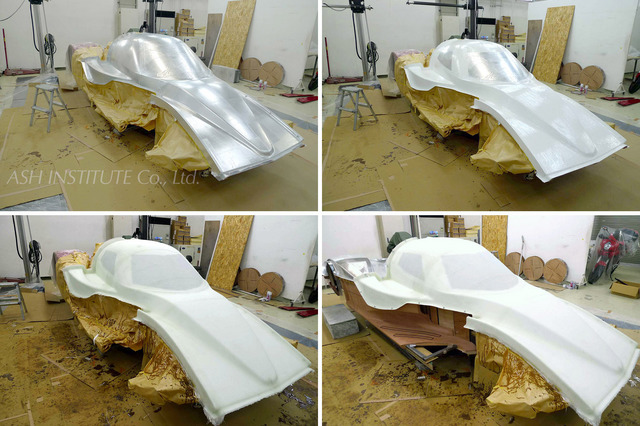
準備が整ったのでいよいよ型取り。
アルミ箔貼って、ゲルコート塗って、FRPを貼り込んでいく。
フロントカウルとキャビン上側を貼ったら、次にリヤカウル。この2号車はこのリヤカウルそのものを
部分改修してそのまま使うのだが、3号車以降のためにこれも型取り。
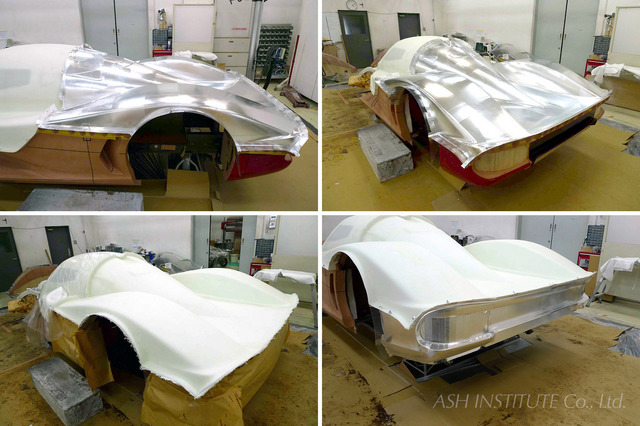
フロントフェンダーは独立したかたまりとして別個に扱う。メインボディの型の硬化を待つ間に型取り
準備を進める。
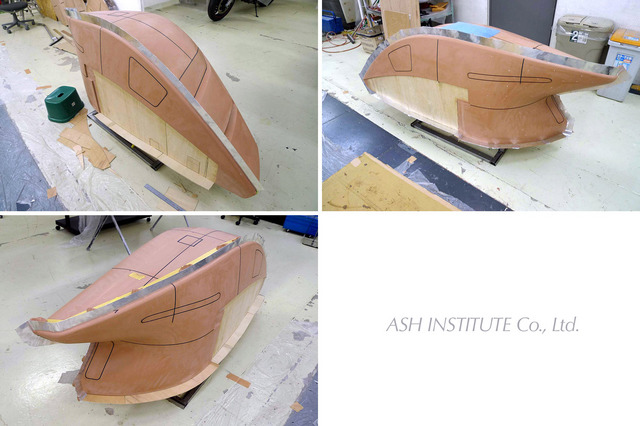
サイドポンツーン前側の型取り前準備。
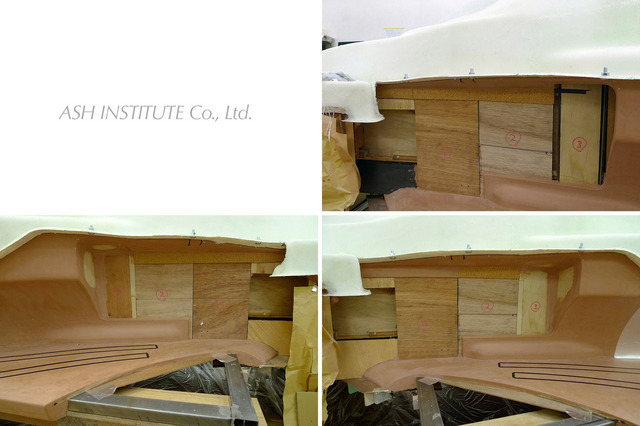
型の分割はこんな感じ。抜き方向を考えつつ、なるべくシンプルに。
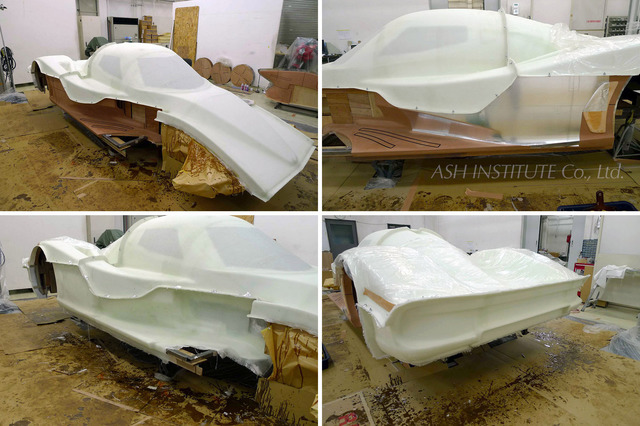
メインボディの成形型の貼り込み、ほぼ終了。
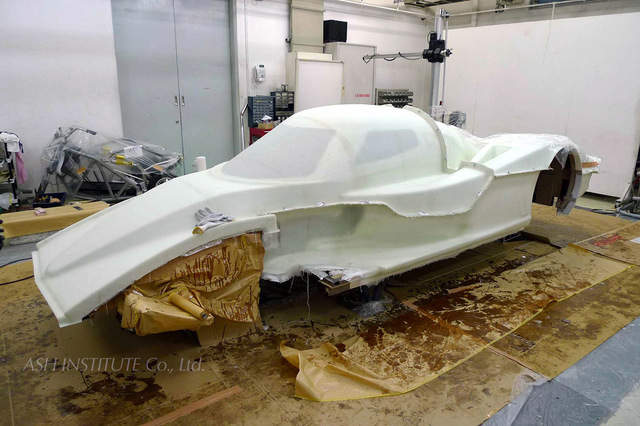
これは何かというと…成形型の補強のための合板を切り出すためのゲージ、にするための1/1スケールの
断面線の図面。イケヤフォーミュラさんにお願いして出力していただいたのだが、あらかじめイケヤ
フォーミュラさんにお願いしておけばクレイモデルのコアでやったのと同じように(あれより全然簡単
だし)レーザーカッターで切り出していただけたはず…。
今回はもう合板をこちらで発注してあったり、私の段取りが悪くてこういう何とも間抜けなことになって
しまい、大きく反省…。
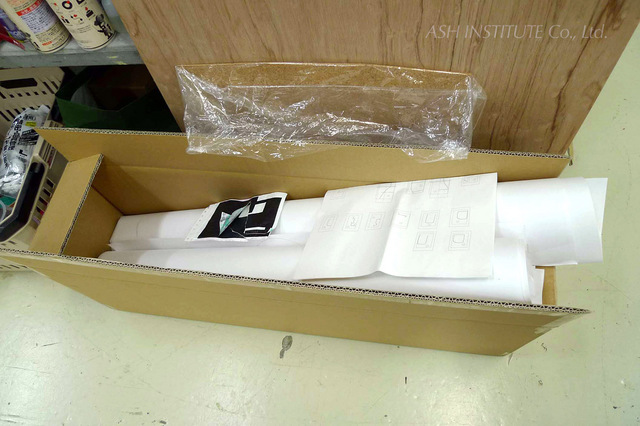
貼り込んだFRP製の成形型の上に切り出した合板をセット。
ボディの貼りこみ作業を行う時にはこれらの型をひっくり返して中に人が入って作業を行うのだが、
その時に床や定盤の上でグラグラしないように、組んだ合板はその上面が1平面で切られたように
揃えられている。
成形型と合板、合板同士をそれぞれFRPで貼りこみ、一体化して、分割部はボルトナットで締結。
あとは硬化を待つ。
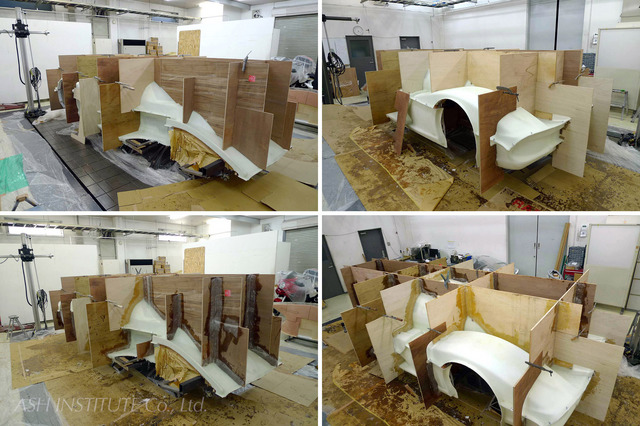
写真は全て、この作業をお願いしている NY Connect の内藤さん撮影。
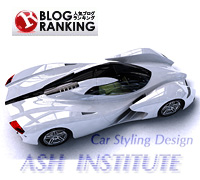
型取り前準備(2016年8月中旬)IF-02RDS ロードバージョン開発経過 [Ikeya Formula IF-02RDS]
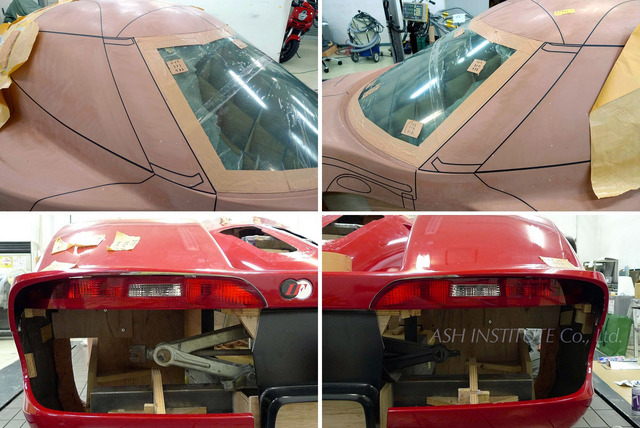
クレイモデルが完成したら次は型取りだが、その準備を色々と。
1号車からキャリーオーバーするリヤカウルも、各エアインテークなどのへこみに、型取りできるところ
よりも深いところにはクレイを詰めてふさいでおく。
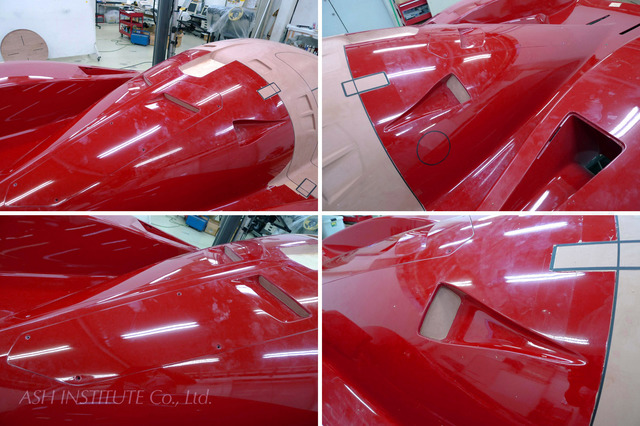
エアガイドフィンが取り付けられる位置にマーキング。
フェンダーアーチは1号車から微妙に修正されているのでそれ合わせてクレイで造形。
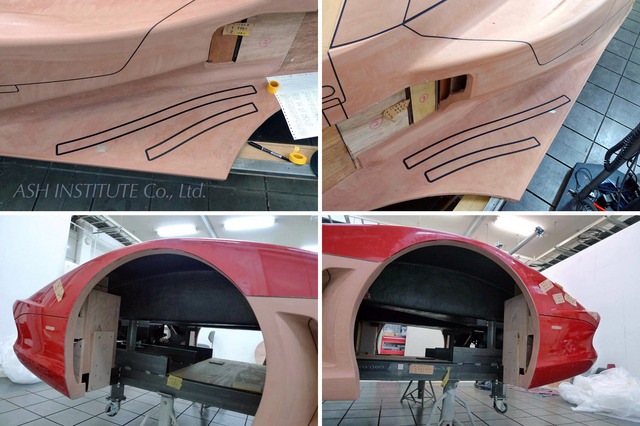
Aピラーとそこに仕込まれるドアヒンジのためのマーキング。
フロントカウルにもフェンダーとの連結に使うパーツや室内のベンチレーションのためのエアインテーク、
そして固定用のファスナーなどのマーキング。
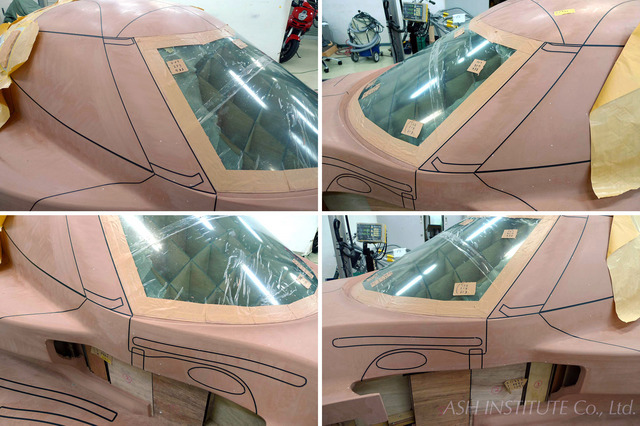
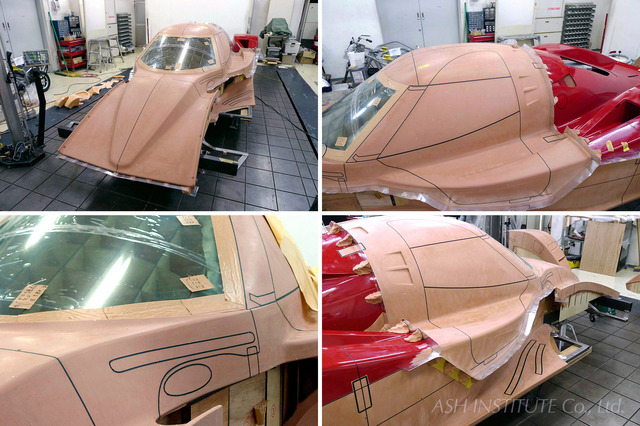
エアインテーク類やライト類のへこみ部分は先にワーカブルを使って型を取って、それを入れ子として成形型に
セットして使う。このワーカブルの表面がラフにでこぼこしているのはわざとで、成形型にセットするときに
このでこぼこに合うようにしか置けないので、位置出しが極めて容易に行える。合理的なやり方。
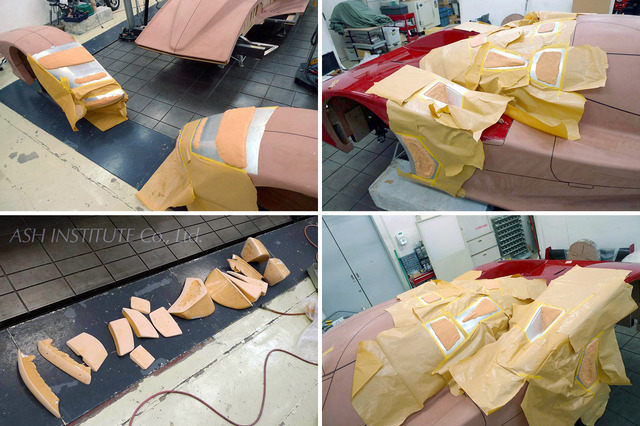
1号車からキャリーオーバーするリヤカウルで、1号車と異なる部分のひとつ、リヤコンビランプ。
シンプルで超薄型、特別にあつらえたかのようにサイズ的におさまりがいい。必要十分な機能を持ち、
もちろん保安基準を満たしている。
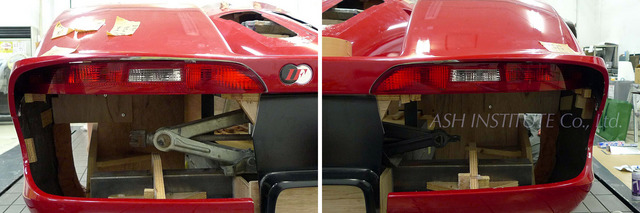
新しいリヤコンビランプは1号車のものよりも車幅方向に大きいので、リヤカウルを少し削ることになる
のだが、そうするとエンブレムの位置がちょっとリヤコンビランプに近すぎて窮屈な感じになるので、
リヤカウルを削った分だけその位置を車両センター方向に移動する。そのため、前の位置にある凹みを
クレイでふさぐ。
リヤコンビライトには十分なマスキングをして、その下側やカウルとの隙間を合板とクレイでふさぐ。
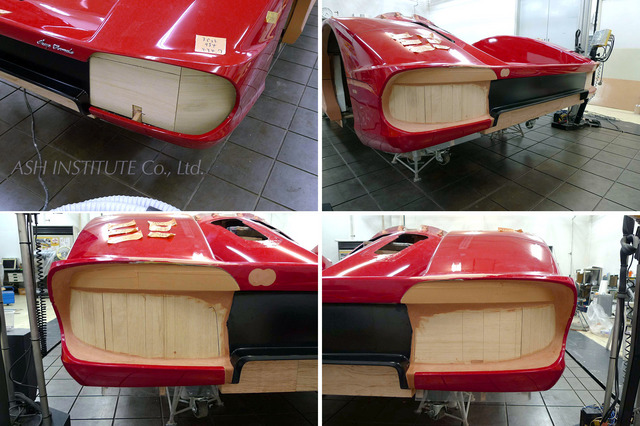
リヤコンビライトを置いたまま型取りするのは、リヤカウルに対しての位置決めをアウターレンズの位置と
角度によって正確に再現するため。成形型にアウターレンズの形状が反映されていればそこにリヤコンビ
ライトユニットを置いて、その状態でマウント用の型を取れるので。
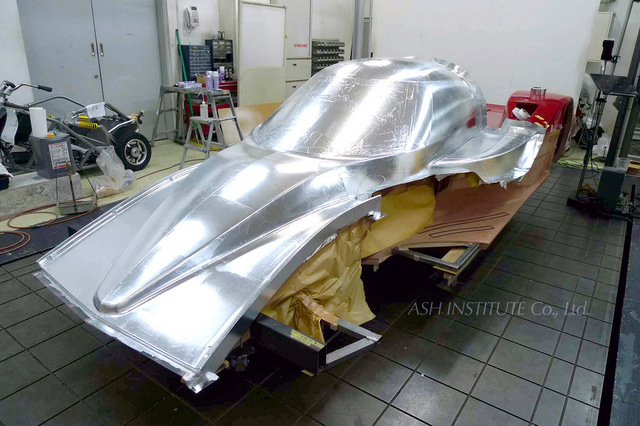
フロントカウルとキャビン上側のクレイの表面にアルミ箔を貼って、最初の型取り用の準備がほぼ整った。
写真は全て、この作業をお願いしている NY Connect の内藤さん撮影。
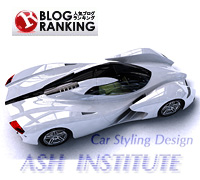